Description
Organized Improvement is one of the management challenges for the 21st century [Drucker 1999] and the twelfth principle of the Agile Manifesto states:
“At regular intervals, the team reflects on how to become more effective,
then tunes and adjusts its behavior accordingly.” [Beck 2001]
This improvement discipline has a name, “Kaizen”. It basically relies on the only way to achieve relentless improvement: everyone at all times should have a Kaizen mindset [SAFe 2021-49].
Reported improvements from Kaizen vary from moderate (25-50%) to significant (75-100%) in different areas such as productivity, Work-In-Process, floor space, throughput, lead-time, set-up time, part travel time, percent on-time delivery, defect rate, or product design [Farris 2006].
Although apparently originating in the U.S. in the 1890s, the concept of Continuous Improvement (CI), or “Kaizen,” is most often recognized as one of the key principles of Japanese manufacturing and, in fact, appears to have been practiced primarily in Japan from the 1950s-1970s, before being reintroduced to the U.S. in the 1980s [Farris 2006]
Kaizen teaches people how to see, think and feel in the context of lean and, ultimately, how to quickly and effectively deploy their improvement ideas [Hamel 2010].
Kaizen is a Japanese word composed of 2 components [Moustier 2020]
- 改: “Kai” - change
- 善: “Zen” - “for the better” or “to take apart” and “to make good”
The ”Zen” part has no relationship with the buddhism practice; they are just homophones.
The English word that is closest to describing Kaizen is “improvement”; however, while improvement is to better your goods and materials, “Kaizen” is to better individuals in a “Let’s make today better than yesterday” mindset [McLoughlin 2017]. This subtlety is so important that in 1984, the Toyota Motor Corporation opened the NUMMI Factory (New United Motor Manufacturing, Inc.) in Fremont, California. Some American NUMMI employees were sent to Japan to learn about Kaizen. When they returned to the United States, they continued to use the word “Kaizen” because they could not find any English words that articulated the concept.
Most of the time, maintenance is perceived as the innovation counterpart. In top-down oriented organizations, innovation is mainly a top management matter while maintenance is delegated to subordinates. Kaizen is something that connects both parts.
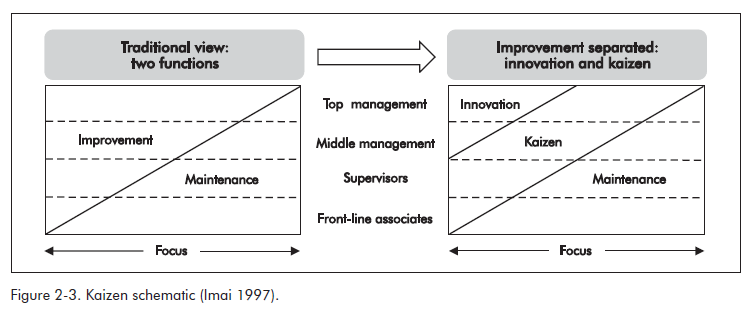
This cultural approach comes from the Edo period (1603–1868) when their way of Kaizen was to increase productivity with each individual’s brain power to generate new ideas, in order to produce much higher quality products by applying creativity to everyday situations and enrich their lives [McLoughlin 2017].
Kaizen is not only about making your work easier; it’s, above all, about improving the quality of your life.
The lineage of Kaizen includes to 2 main sources which originated in the United States [Hamel 2010]:
- the Training Within Industry (TWI) initiative - established in 1940 for the purpose of increasing U.S. wartime production output
- the plan-do-check-act (PDCA) cycle - developed as early as 1939 by Walter Shewhart and taught in Japan by W. Edwards Deming starting in 1950
These two seeds of kaizen were developed at almost the same time in the United States and then planted in Japan after World War II.
Many plants followed this improvement cycle [Hamel 2010] as an Internet meme:
- PTRS - Toyota’s version of PDCA with slightly different terminology for Plan-Try-Reflect-Standardize
- DMAIC - Define-Measure-Analyze-Improve-Control
- SDCA - Standardize-Do-Check-Act
Since there is no improvement without standard work, SDCA can also be viewed as a complement to PDCA [Hamel 2010] as in a 5S approach. This combination may then be viewed through the lenses of a hierarchical organization where the Top Management tries to improve the company through a PDCA cycle and a SDCA is then arranged in tandem to consolidate the decisions from the hierarchy.
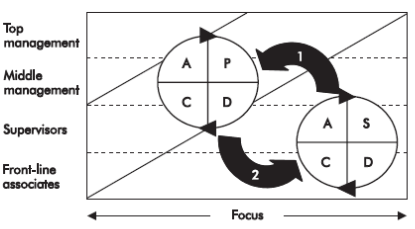
Why kaizen works:
- Kaizen is driven by pragmatism and Lean Leaders want to generate some quick short-term wins [Hamel 2010]
- Focusing short-term wins creates a sense of urgency [Kotter 2008] and leads people to a “Don’t wait—do it now!” state of mind since time is key to minimize an issue [McLoughlin 2017]
- While big changes can be frightening, small steps disarm the brain fear response and let rational thoughts and creativity drive your decisions; then your resistance to change weakens instead of the “fight-or-flight” response [Maurer 2014]
- Small step do not require efforts [Maurer 2014]
- “Improve by 1% a day, and in 70 days you’re twice as good” [Cobb 2011]
- Grand strategy can wait until there is some meaningful momentum [Hamel 2010]
Since your brain is not inclined to improve or change, the small regular training of your mind and body helps create a brain that is more accustomed to long-term delayed gratification activities and, therefore, more inclined to improvement and change through effort. Self-discipline facilitates kaizen [Medinilla 2014]. This mindset is reflected in the Japanese saying “一日一歩” : One day, one step [Frola 2021].
The Kaizen philosophy can be summarized in 10+1 principles [Hamel 2010]:
- 1: Thinking PDCA and SDCA
- 2: Going to the Gemba, observe and document reality
- 3: Spotting the root cause by asking 5 times “why?”
- 4: Being dissatisfied with the status quo
- 5: Kaizenning what matters
- 6: Having a taste for action
- 7: Driving sustainable improvement through frequent, small incremental changes to achieve big enhancements
- 8: Using creativity and be resourcefulness
- 9: Involving everyone to get into Kaizen
- 10: Transforming leadership to impulse change
+ Do everything with humility and respect for the individual
The difficulty with Kaizen in projects is that on the one hand, almost everything can be improved, and on the other hand, most local improvements do not translate into better project performance [Cox III 2010]. This is why it is important to be able to experiment with those improvement attempts until something provides a sensible progress.
There are also some known symptoms of Kaizen malpractice [Hamel 2010]:
- 1. Variation of the practices in wrong directions
- 2. Insignificance of some events
- 3. Incoherence then no synergy
- 4. Blindness to wastes (Muda)
- 5. Indifference to wastes as a filter to Kaizen
- 6. Lethargy from supporting Teams - their sense of emergency is inadequate
- 7. “Unsustainability” of Kaizen gains due to lack of notably validation, rigor, development, training, discipline
- 8. Demoralization due to lack of meaningful and sustainable results, inadequate planning, resources, empowerment, recognition
- 9. Presumption - see Cargo Cult effect.
and a top 10 of the reasons why Kaizen fails [Medinilla 2014]:
- Absence of a real culture
- Politics and blame games
- General resistance to change
- Lack of momentum
- No sense of ownership, no empowerment
- Short-term vision
- Failure to identify problems
- Failure to see root causes
- Failure to plan and execute - notably due to people's commitment to project deadlines, no time to deliberate practice, learning, experimenting or sharing knowledge with each other.
- Lack of resources
Kaizen must be done with Empowered People and not to people. Because of people's implication, Kaizen events (see here under) have the potential to produce more favorable technical and social system outcomes than “traditional” organization [Farris 2006].
Kaizen should be executed at all levels of the organization, from the president to the janitor.
However, if
- managers decide not to let people do Kaizen because they think their employees don't have the ability to implement Kaizen,
- and people decide not to even try because their superiors tell them their ideas aren't needed,
then there is no way to attract new, innovative, and creative ideas into the company to improve your business. Therefore, the foundation of Lean management is, trusting people to encourage each individual to suggest ideas for the purpose of achieving collective creativity and solving problems [McLoughlin 2017].
There is no Kaizen without real collaboration of every employee [Medinilla 2014] because everyone’s involvement is necessary to solve systemic issues [Appelo 2010] [Senge 2010]. As the Japanese say, “One step forward by 100 people is better than 100 steps by a single person” [McLoughlin 2017].
The “Toyota Way” towards improvement claims People are as important as CI [McLoughlin 2017].
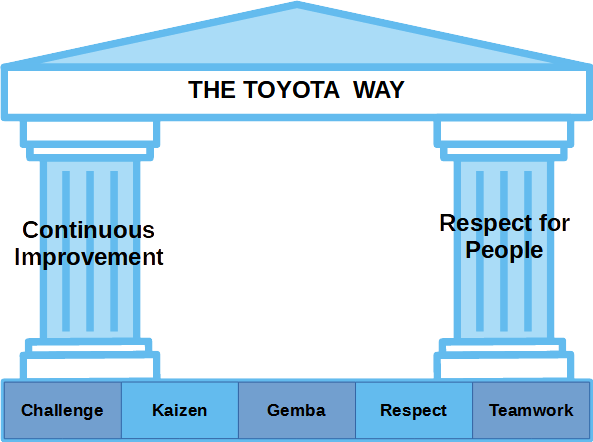
The thing is, improvement generates negative emotions in key individuals at all levels of an organization (eg. frustration, impatience), along with achievements. Therefore, a combination of analytic and emotional intelligence is required [Hamel 2010] because moods can also help Kaizen events; for instance, each day of the event, a mood level such as the Niko-niko, or a scoring from 0 to 10, can be used to see how satisfied involved people feel about the event. You may also use the Emotion Roadmap(™) [Hamel 2010] that will help you to take feelings into account to drive decision making along with technical and plan improvement.
Because Kaizen workshops also aim to focus on using human knowledge and creativity [Farris 2006], this approach will help to build improvement in a trustful environment to build trust before you begin to make any changes [McLoughlin 2017]. While many “traditional” improvement projects end with a set of recommended changes presented to senior management, Kaizen teams are generally given the authority to implement solutions as they are developed, without direct approval of each change from management [Farris 2006].
Hamel provides a transformational leadership model through a combination of humility, respect, competency, trust and credibility to build engagement and growth with technical change to lead cultural change to achieve great results [Hamel 2010].
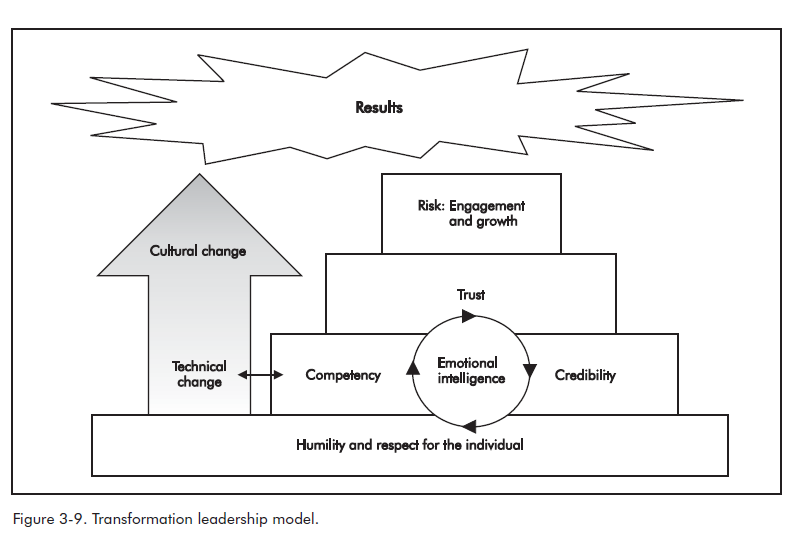
The cultural change generated by Kaizen infers [Medinilla 2014]:
- A deep purpose for the People: if you are going to ask your people to excel and improve, to put their energy into making something awesome, you need to show them a noble cause, a global purpose beyond profits, company growth, and stakeholder wealth—who would really care about those?
- A long-term vision to drive People in a consistent direction
- A whole system approach
- A constant communication
- “Quality first” mindset
- A sense of recognition from the organization
- The Agile Manifesto values [Beck 2001]
- Active ongoing encouragement from the leadership to keep the Kaizen mindset alive.[Larman 2010]
Every lean and agile process has a feedback loop . Without feedback there is no kaizen. If management is calling itself agile but refusing to let the team “waste time” on retrospectives, we risk losing the kaizen benefits of the agile feedback loop [Freedman 2015].
Kaizen should take place at every level of the company:
- People Kaizen: everyone should improve [Medinilla 2014] [Drucker 1999] notably in a follow-break-transcend the rule Shu-ha-ri progression
- Team Kaizen: Improving the Teams who make your stuff [Medinilla 2014] - people may conflict with Teams because they are more concerned about being right than agreeing with something - Teams may conflict, and they prefer to pass on uncomfortable issues (the “status quo”) so these conflicts are neither addressed, nor improved. Therefore, you have to start worrying about People and think in terms of Team Growing rather than Team Building.
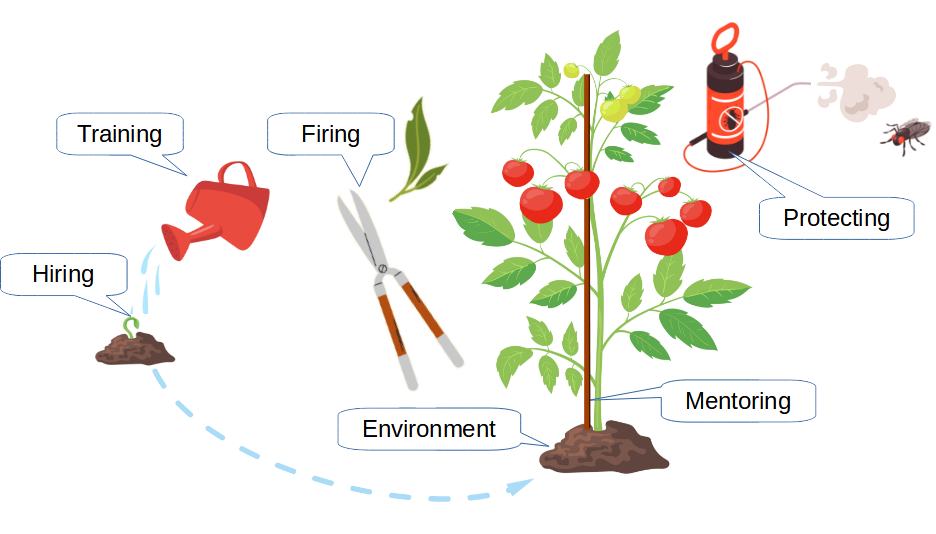
- Process Kaizen: Improving the Way You Do Your Stuff [Medinilla 2014][Freedman 2015] [Drucker 1999]
- Product Kaizen: Improving the Stuff You Make [Medinilla 2014][Freedman 2015] - Knowing your Client is knowing your product [Medinilla 2014]
- Retrospectives and Kaizen Events: Improving the Way You Improve [Medinilla 2014]
Kaizen proposes a quite formal way to improve the organization thanks to [Hamel 2010]
- Specific workshops
- A Kaizen Promotion Office with full-time coordinators/facilitators [Farris 2006] to avoid pitfalls and to provide both material and emotional (eg. encouragement, active participation, mentoring, and holding people accountable) support across the organization
- Kaizen centered people such as evangelists, change agents such as early adopters, Kaizen champions from the management and leaders in Teams [Medinilla 2014]
- A Kaizen Community of Practice
A Kaizen workshop triggers a lot of things such as [Farris 2006]
- enthusiasm from employee’s participation
- “buy-in” to the changes made during the event
- creation of a belief that change is possible
- increased employee empowerment
- commitments from employees to the improvement program over the longer term
- improved employee attitudes toward work
- increased cross-functional cooperation
- support for creating a learning organization
- development of a culture that supports long-term improvement
- creation of a “hands on” and “do-it-now” sense of urgency [Kotter 2008]
for change/improvement in the entire facility - employee pride in accomplishments made during the Kaizen event.
Therefore, Kaizen can be viewed as an investment in employee training [Farris 2006]. It also avoids the Hawthorne effect, a real life experience at the Hawthorne plant, that demonstrated in the early 1930’s that environmental changes did not last long since changes came from above.
To organize improvement, Kaizen is impulsed by different kinds of workshops [Hamel 2010]:
- "Kaizen event" also known as “rapid kaizen”, “breakthrough kaizen”, “Gemba kaizen”, “kaizen workshops“, “short cycle kaizen” or “Kaizen Burst” (“burst” comes from the peaks you may see in a Value Stream Mapping [Poppendieck 2006] [Moustier2020] [Learn Lean 2020] which require to be flattened to prevent production irregularities
- Kaizen Blitz - In German, “Blitz” means “lightning” and refers to a war strategy based on very fast moves. A Kaizen Blitz lasts between a few minutes to a couple of days. It is involved when you know what to change and no pre-work is required. It follows the sequence of DMAIC [IsSixSigma 2022-1]
- Daily kaizens: every day, everyone in the organization is involved in making small changes that can be made and reviewed within the Team under few hours or few days
Let’s refine the most significant component of Kaizen implementation, the "Kaizen event". While the engine of any lean transformation is people, the kaizen event is engaging the hearts and minds of the workforce. [Hamel 2010]. This is a 3-5 day workshop that is directed toward a specific goal [Dolcemascolo 2022] - it requires notably [Farris 2006]
- a charter - displayed in the event room to keep people aligned
- 5-8 cross-functional team (CFT) of employees solely dedicated to the event for its duration - CFTs enable the “good chemistry” to mix environmental, design, task design, group design, group processes, and group psychosocial traits factors. CFTs are a mix of skills and backgrounds, with half coming from the target area [Farris 2006].
- the scope of the problem to fix - improvement goals are set in advance by organizational leadership
- an allocated budget limit to fix the problem to solve in order to focus on low-cost changes, rather than changes requiring significant capital investment
- a problem statement extracted notably in a 5W approach
The classic agenda of such a workshop is [Learn Lean 2020-1] [Learn Lean 2020-2][IsSixSigma 2022-2]:
- day 1: introductions / why we are here / charter reviewing / problem definition agreement / process map / data reviewing / data organization for analysis
- day 2: prev. day recap / defining solution / testing solutions
- day 3: prev. day recap / extra testing / solution monitoring for positive results
- day 4: prev. day recap / check for adjustments - Kaizen Teams are encouraged to achieve more than one cycle of solution refinement [Farris 2006]
- day 5: prev. day recap / celebrate the achievement to emotionally anchor the outcome with the event
Every 2 – 3 hours, team reassembles in Kaizen event room to review progress and then returns to the target work area [Farris 2006]
To set up the event, about 5 weeks before, you need to make sure you have
- some agreement on who will be in charge of the event to make the decisions
- the right people to involve in the workshop
- a suitable location to bring everyone together and allow for team meetings
- workshop materials for everyone (whiteboards, pens, network, ...)
- catering and accommodation
Once the Kaizen event is over, there are still some post-event actions to be done in order to anchor its outcome and benefits and propagate the momentum generated by the event:
- Some communication on the outcome to promote lessons learnt [Farris 2006]
- A follow-up plan must be designed before the change and observed with strong discipline after it, thus making the improvement more continuous over time.[Medinilla 2014]
Most of the time, a Kaizen event is not a single, isolated improvement mechanism, but something which happens very frequently – dozens, or even hundreds of times per year when it comes to big organizations [Farris 2006]
Less iconic than the Kaizen Event but probably more important, the “Daily Kaizen” is the master key to do Kaizen. It consists in [Kaizen Institute 2013]:
- Monitoring process standards
- Identifying deviations from the standards
- Easy problem solving in order to achieve standards
- Easy problem solving in order to raise the standard
- Reflecting, learning and skill building
This immediate feedback loop is particularly adapted to complex (Cynefin wise) environments. It [Kaizen Institute 2013]
- Ensures the alignment of objectives in the whole organization;
- Improves the flow of material, information and the state of mind to increase team productivity;
- Creates mechanisms for quick problem solving;
- Helps to create standards;
- Reduces the impact of uncertainties on day-to-day basis;
- Supports the improvements made in projects;
- Fosters the creation of a CI culture.
The transition to kaizen readiness is notably enabled by [Hamel 2010]:
- A “Sensei” guidance, to coach teams in identifying problems and impediments as well as product ideation by including notably agile practices
- effective transformational leadership
- solid short-term wins
and a lot more factors gathered in [Farris 2006] from page 47 regarding
- Task Design Factors
- Group Composition Factors
- Organizational Context Factors
- Internal Process Factors
- Kaizen Event Program Characteristics
Impact on the testing maturity
Kaizen is the cultural root of Lean and therefore at the heart of agility [Medinilla 2014]:
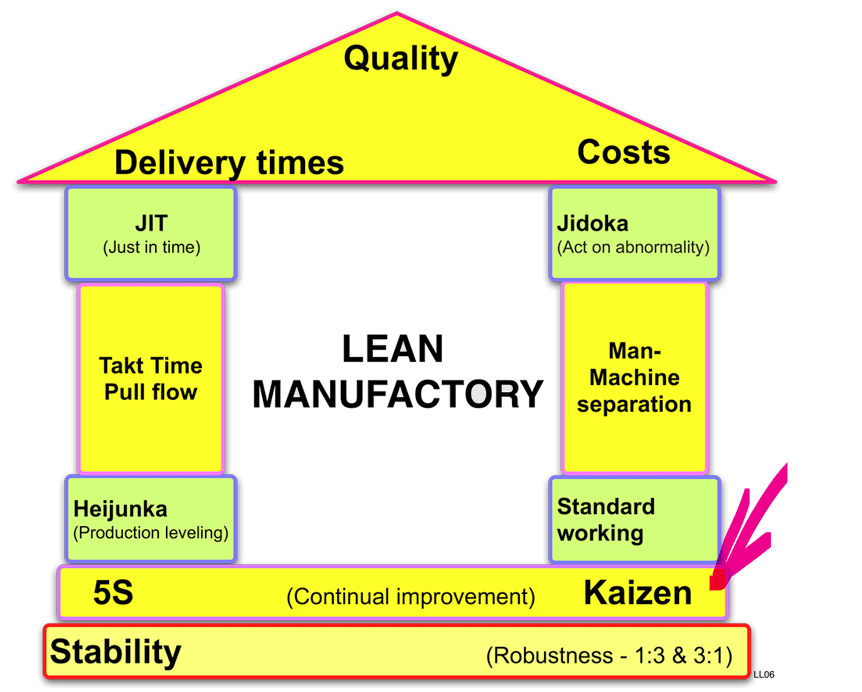
- Kaizen is about change and improvement and responding to it instead of blindly following existing plans.
- Kaizen talks about empowerment and motivation—creating self-organizing teams and trusting them to get the job done.
- It talks about continuous attention to excellence.
- It's also about empowerment, motivation by creating self-organized teams, trusting them to get the job done with a continuous focus on excellence and removing waste to maximize the amount of work not done.
- It talks about meeting at regular intervals and reflecting (in Japanese Hansei) on how to become more effective and then tuning and adjusting behaviors accordingly. [Medinilla 2014]
- Cross-Functional team-based organization facilitate
- Self-organizing & empowered
- Constant communication is intrinsically part of Kaizen and agility
- Transparency is required to enable both
- The absence of fear to enable innovation
- Courage is required in Kaizen and is also a value of Extreme Programming [Beck 2004]
- Kaizen is about change and change is a part of Manifesto
- Small increments is promoted in product ideation and so in Kaizen regarding improvements; the CI is therefore at the core of Agile - this draws an obvious parallel between Agile constant delivery of product increments and Kaizen constant delivery of small, cumulative, evolutionary improvements
- Kaizen comes from a background much broader than process re-engineering or removing impediments; this is the usual explanation from the Lean and Agile worlds.
- Kaizen and agility evolutions have no end but the unattainable, perfection. [Freedman 2015]
- Two good examples of Kaizen in Agile environments are Retrospectives and Refactoring
- While collaboration, customer focus, self-managed teams, and kaizen originate in lean, the Agile Manifesto and Principles originally evolved to correct deficiencies in predictive software development [Freedman 2015]
- Scrum and lean thinking encourage inspection & adapt [SAFe 2021-49] practices with a kaizen mindset, rather than formulas or cookbook recipes for workplace practices and processes [Larman 2010] for there are simply bootstraps to improvement
- Kaizen events is quite close to the PI Planning event in SAFe [SAFe 2021-32]
All those parallels actually show that Kaizen embodies the agile Manifesto [Freedman 2015]. Kaizen also faces the same needs as agile, such as convincing everyone that Kaizen is, in fact, a culture and not some kind of process, tool, or framework.
This common barrier regarding change has been studied by Chris Argyris with his “theory of action” which states we have 2 drivers:
- type I: a productivity reflex
- type II: a defensive reflex
While type I aims for CI, type II comes to bridle the productivity reflex with impediments based on cultural and addictive approaches such as:
- “We are used to doing it this way”
- “In the past, we tried and badly failed”.
Struggling against type II is like facing a ceiling glass that prevents improvement. Sometimes, to overwhelm this ceiling, you need some breakthrough instead of CI: “Kaikaku” (改革), a reform, an invite to stop and literally hit the issue with a strike on an animal hide as inform the several parts of the kanji signs.
In Japanese Kaikaku is a radical improvement: a change in one strike, as opposed to Kaizen which happens in many small incremental improvements.
Sometime, Kaikaku is required:
“If I had asked people what they wanted, they would have said faster horses.” – Henry Ford [Vlaskovits 2011]
This famous quote can be easily faced when the Teams reaches a ‘local maximum’. To continue improving, the Teams need to radically change something.
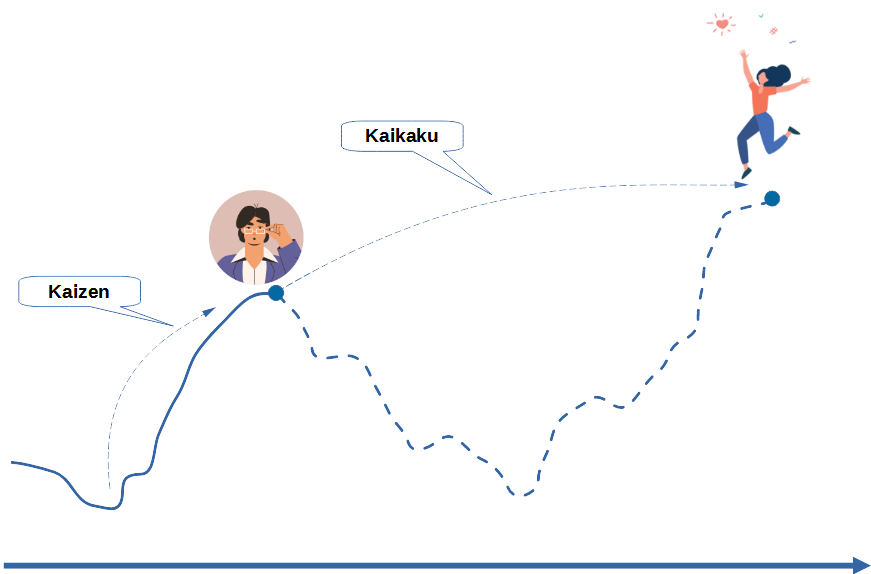
Kaizen agents, such as Scrum Masters or Agile Coaches, are here to detect local maxima and let Kaikaku happen within the Teams. This is mostly made possible because those Kaizen agents are neither directly contributing to delivering products at the end of the iteration nor they are responsible for project deadlines [Medinilla 2014].
The Kaikaku approach is traumatic by nature because change is always hard. However, radical change might be too hard for some cultures. No matter how seductive the ‘one-shot fast change’ idea might be, change is always unconsciously perceived by the human mind as an aggression, and a big aggression might not be well understood even for the most rational mind.[Medinilla 2014].
Coming back to Argyris, breaking the type II ceiling glass, can happen through understanding with some “awareness sessions” and workshops or a drastic and sudden change.
The late option is sometimes preferred to awareness and workshops when it is so difficult to naturally improve. A favorable climate to such a style of change can be a sense of a “burning platform” [SAFe 2021-50] [Kotter 2008] which will draw people to take the effort, investment, and risks to go for Kaikaku [Medinilla 2014].
If you assume that things are alright the way they are, you can’t do kaizen. Therefore, to improve testing, some assumptions from testing standards in which possible status quo need to be challenged [Larman 2010] [Moustier 2020] :
- Assuming testing means “testing” - “Testing requires finished code and is only reviewing some release candidates through the UI” may not be alway relevant; it can take on different aspects such as reviewing User Stories before being developed, code review, a better design
- Separating development and testing notably through a Test department
- TMM, TPI, and other ‘maturity’ models
- Blindly trust ISTQB and other tester certifications
- Separate test automation team
- Using defect tracking systems for any issue - during the iteration, it is better to focus on doing everything at the same time rather than introducing a record that will create delays and WIP (Work In Progress)
- Commercial test tools that may both raise and limit your testing maturity - your trust in those expensive tools must be under your people control, not the Vendors’
- Traditional requirement handoff or a “No spec, no test” mindset
- Testing requires a defined and approved test scenario
- Thinking ATDD is for testers
- Confusing TDD and ATDD
- “Optimizing” the requirements workshop with fewer resources to maximize people utilization
- Multiple requirement descriptions - tests act as the living documentation of the requirements and additional documents for the same requirements are probably redundant waste.
- Keeping test cases in a safe, just in case they would reveal some regression one day
- Traceability to “discover which tests need to be run when a certain requirement changes” - An alternative is to automate all tests so they can all be run, eliminating thus the traceability need
- Automate all test cases - 100% automation may lead you to very expensive tests
- Handling non-functional testing differently from functional testing
- Testing is always a step-based process (write → run → report → 5S)
- Testing requires a Test Manager to make things consistent - try mixing product management and quality matters
- Testing must be finished before releasing time
- Testing must be based on a policy, a strategy and a "master plan" [ISTQB 2018]
- Testing coverage is key and a 100% achievement is key
Kaizen is the main engine that will allow companies to transform and face the "software and digital era", the revolution that is taking place before our eyes [SAFe 2021-51]. This is why Kaizen is considered one of the management challenges of the 21st century [Drucker 1999]
Agilitest’s standpoint on this practice
Click here to ask for the standpoint of Agilitest.
Related cards
To go further
- [Appelo 2010] : Jurgen Appelo - « Management 3.0: Leading Agile Developers, Developing Agile Leaders » - Addison Wesley - 2010 - ISBN : 978-0321712479 - voir aussi https://fr.slideshare.net/jurgenappelo/agile-management-leading-teams-with-a-complex-mind/
- [Beck 2001] : Kent Beck et al. - « Manifeste pour le développement Agile de logiciels » - 2001 - http://agilemanifesto.org/iso/fr/manifesto.html
- [Beck 2004] : Kent Beck & Cynthia Andres - feb 2004 - “Extreme Programming Explained: Embrace Change” - ISBN : 9780321278654
- [Cobb 2011]: Jeff Cobb - 2011 - “The 1% Solution for Learning Growth - Mission to Learn - Lifelong Learning Blog” - https://www.missiontolearn.com/one-percent-solution/
- [Cox III 2010]: James F Cox III & John Schleier - “Theory of Constraints Handbook” - isbn:9780071665551
- [Dolcemascolo 2022]: Darren Dolcemascolo & Jonathan Trout - c2022 - “Kaizen Events: When and How to Use Them” - https://www.reliableplant.com/Read/8904/kaizen-events
- [Drucker 1999]: Peter F. Drucker & John White - “Management Challenges for the 21st Century” - isbn:9780887309984
- [Farris 2006] : Jennifer A. Farris - “An Empirical Investigation of Kaizen Event Effectiveness: Outcomes and Critical Success Factors” - https://www.semanticscholar.org/paper/An-Empirical-Investigation-of-Kaizen-Event-Outcomes-Farris/346430baf07062911b9a9b8ec068b0d53f714ac7
- [Freedman 2015]: Richard Freedman - “The Agile Consultant: Guiding Clients to Enterprise Agility” - isbn:9781430260523
- [Freepik]:
* pch.vector at Freepik - https://fr.freepik.com/vecteurs-libre/cycle-croissance-illustration-du-plant-tomate_16369137.htm and https://fr.freepik.com/vecteurs-libre/heureux-jeune-couple-s-amusant-fille-mec-dansant-fete-celebrant-illustration-plate-bonnes-nouvelles_11235596.htm
* Freepik - https://fr.freepik.com/vecteurs-libre/collection-elements-du-jour-tonnelle-plate_23871194.htm
* macrovector at Freepik - https://fr.freepik.com/vecteurs-libre/icones-isometriques-du-service-desinfection-antiparasitaire-equipement-equipe-exterminateurs-professionnels-cafard-rat-fourmi_7379199.htm
* redgreystock at Freepik - https://fr.freepik.com/vecteurs-libre/portraits-plat-avatar-effraye-choque-visages-personnages-excites-etonnes-jeunes-bouche-ouverte-confus-perplexe-homme-femme-etonnes-emotions-effrayees-personne-horrifiee_23624508.htm - [Frola 2021]: Michelle Frolla - “69 wonderful japanese idioms that will brighten your day” - https://www.theintrepidguide.com/japanese-expressions-and-idioms/
- [Hamel 2010] : Mark R. Hamel - “Kaizen Event Fieldbook: Foundation, Framework, and Standard Work for Effective Events” - isbn:9780872638631
- [IsSixSigma 2022-1]: www.isixsigma.com - “Kaizen Blitz” - https://www.isixsigma.com/dictionary/kaizen-blitz/
- [IsSixSigma 2022-2]: www.isixsigma.com - “Kaizen Event” - https://www.isixsigma.com/dictionary/kaizen-event/
- [ISTQB 2018] : ISTQB - 2018 - “Certified Tester Foundation - Level Syllabus” - https://www.istqb.org/downloads/category/2-foundation-level-documents.html
- [Kaizen Institute 2013]: Kaizen Institute - 2013 - “Daily Kaizen” - https://kaizeninstituteindia.wordpress.com/2013/08/03/daily-kaizen/
- [Kotter 2008]: John P. Kotter - “A sense of urgency” - ISBN: 9781422179710 - https://archive.org/details/senseofurgency0000kott/page/n7/mode/2up
- [Larman 2010] : Craig Larman, Bas Vodde - « Practices for Scaling Lean & Agile Development - Large, Multisite, and Offshore Product Development with Large-Scale Scrum » - Addison-Wesley - 2010 - ISBN-13: 978-0-321-63640-9
- [Learn Lean 2020-1]: Learn Lean - JAN-2020 - “Lean Kaizen Event (for Quick Wins)” - https://www.youtube.com/watch?v=igYxzmqe1A0
- [Learn Lean 2020-2]: Learn Lean - OCT-2020 - “6 Step Kaizen Process (Plus BONUS)” - https://www.youtube.com/watch?v=gEC-81b7bdc
- [Lieshout 2006] : Laurens van Lieshout - JAN 2006 - “Lean manufactory house” - https://commons.wikimedia.org/wiki/File:Lean_manufactory_house.png?uselang=fr
- [Maurer 2004] : Robert Maurer - “One Small Step Can Change Your Life: The Kaizen Way” - isbn:9780761181347 - https://www.youtube.com/watch?v=VHkOFs67d9A and https://www.youtube.com/watch?v=DmgIgTMqGdU
- [McLoughlin 2017]: Collin McLoughlin & Toshihiko Miura - “True Kaizen: Management's Role in Improving Work Climate and Culture” - isbn:9781351719124
- [Medinilla 2014]: Angel Medinilla - “Agile Kaizen: Managing Continuous Improvement Far Beyond Retrospectives” - isbn:9783642549915
- [Moustier 2020] : Christophe Moustier – OCT 2020 – « Conduite de tests agiles pour SAFe et LeSS » - ISBN : 978-2-409-02727-7
- [Poppendieck 2006] : Mary Poppendieck & Tom Poppendieck - SEP 2006 - “Implementing Lean Software Development: From Concept to Cash” - ISBN 9780133812848
- [SAFe 2021-32] : SAFe - FEV 2021 - “PI Planning” - https://www.scaledagileframework.com/pi-planning/
- [SAFe 2021-49]: SAFe - FEV 2021 - “Inspect and Adapt” - https://www.scaledagileframework.com/inspect-and-adapt/
- [SAFe 2021-50]: SAFe - SEP2021 - “Reaching the Tipping Point” - https://www.scaledagileframework.com/reaching-the-tipping-point/
- [SAFe 2021-51]: SAFe - JUL2022- “Business agility” - https://www.scaledagileframework.com/business-agility/
- [Senge 2010]: Peter M. Senge - 2010 - “The Fifth Discipline: The Art and Practice of the Learning Organization” - isbn:9781407060002 - see also 11 Laws of the Fifth Discipline
[Vlaskovits 2011]: Patrick Vlaskovits - 2011 - “Henry Ford, Innovation, and That ‘Faster Horse’ Quote” - https://hbr.org/2011/08/henry-ford-never-said-the-fast